Flexible Three-Module In-Pipe Climber
Flexible In-Pipe Climber
Flexible In-Pipe Climber
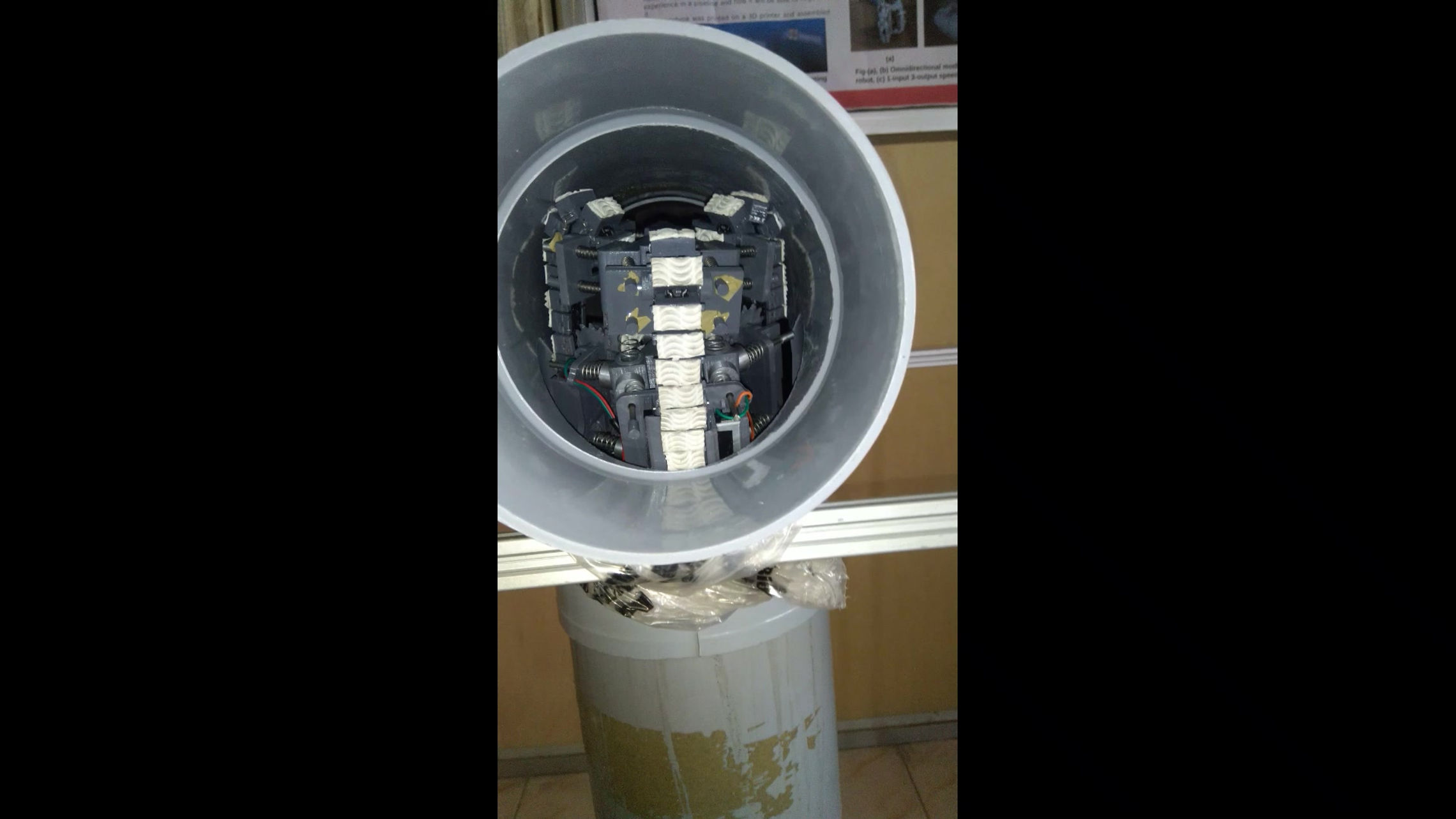
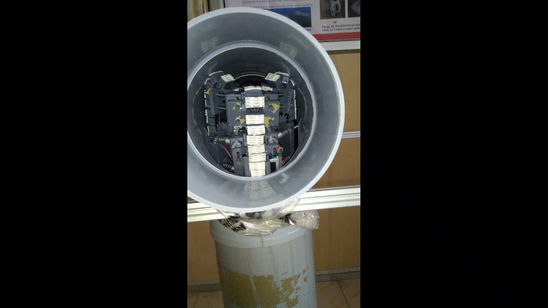
T-junction Negotiation

Overcoming Motion Singularity in Pipe Junctions
OBJECTIVE
Networks of pipelines are ubiquitous and are under use continually. In modern cities, with increasing penetration in rural areas, they guide the flow of liquids and gases - like oil, water, chemical vapors, sewage and other items. Since pipes are generally opaque and the network is laid underground - it makes the pipes inaccessible for any manual inspection from its inside or outside. Hence, they are frequently damaged by clogging, corrosion, crack propagation and scaling by chemicals.
Thus, we have undertaken this task, i.e., build robots which could inspect these pipes. Such mundane but necessary precautionary measures can reduce the chances of failures, ranging from minor leaks to catastrophic ruptures. They also rule out the possibility of human error and negligence. The larger aim of the product would be providing solutions to the industrial plants as well.
DESIGN
The 3 track/module pipe climber has been proven to be dynamically more stable and superior compared to an increased number of tracks. The tracks of the robot are symmetrical and at equal angles with each other. The pipe climber has been so designed that it can work against the gravity also. This is possible with the help of traction generated by the rubber on the 3 tracks against the interior of the pipe. The modules are pressed against the wall radially outwards from the robot. This presses the track and helps it hold onto the inner wall of the pipe.
Though there has been considerable research in this field, the major problem lies in negotiating junctions, especially when the turns are sharp. Single body robots have been unable to do it without altering the orientation of the robot or adding accessories for this specific purpose.
​
Inspired by the flexibility in human bodies, we have designed and prototyped a robot that can negotiate such junctions with inherent compliance. Rigid robots lose contact in some situations and the motion of the robot ceases - leading to 'motion singularity'. Hence, with added flexibility, the robot can stretch from one side and compress from the other to completely dismiss the possibility of contact loss.
​
​
HARDWARE
The pipe climber requires high torque motors, one for each module. The high torque requirement is due to the traction, load and gravity the robot has to overcome to move as desired. The tracks have sprockets that act as idlers for the motion of the track along the inner walls of the pipe. Motors should also be small in size so that they can be used inside small diameter pipes. Considering all these factors, Micro-metal Gearmotors were chosen. Specifications:
​
-
Gear Ratio = 1000:1
-
Volatage = 12V (High Power Carbon Brushes)
-
Dimensions = 10 x 12 x 30 cubic millimeters
-
RPM(max) = 18
-
Torque(max) = 10kg-cm
​​
The body of the robot is completely modular and has been 3D printed using PLA and ABS. The design is done on SolidWorks and the dynamics of the machine has been analysed using MSC ADAMS. The flexibility of the robot and its modules are provided using springs of varied stiffness and universal joints. Sensors are placed in the front which help the robot guide its path. The primary sensor used is Ultrasound Sensor.
CONTROLS
The robot is controlled using a microcontroller - Arduino uno. The 3 motors are connected to an L298D motor driver which is used to provide speeds to the individual modules. For negotiating bends and junctions, the motors were given differential speed, i.e., the modules on the inner sides of the bends are given lesser speed and the modules away from the turn are given higher so that both move concurrently in an arc and complete the turn. Obviously, the outer modules have to move a larger distance compared to inner ones. The logic for this differential is coded in the micro controller itself.
** The research has been accepted in an IEEE conference and details of the project will be updated as soon as it is published